Info from
Our wonderful Climate Commission Planners, aka CCP, have decided that we are all going to drive electric vehicles (EVs) in the next few years. We know there is not enough electricity to power their dreams but they could copy a plan for that eventuality. However, they assure us that once we are all driving EVs we will save the planet. But save it from what? Certainly not from environmental destruction on a monumental scale.
Read on to see what the Manhattan Institute has calculated. (Sorry about the US pounds.)
A lithium EV battery weighs about 1,000 pounds.(a) While there are dozens of variations, such a battery typically contains about 25 pounds of lithium, 30 pounds of cobalt, 60 pounds of nickel, 110 pounds of graphite, 90 pounds of copper(b), about 400 pounds of steel, aluminum, and various plastic components.(c)
Looking upstream at the ore grades, one can estimate the typical quantity of rock that must be extracted from the earth and processed to yield the pure minerals needed to fabricate that single battery:
• Lithium brines typically contain less than 0.1% lithium, so that entails some 25,000 pounds of brines to get the 25 pounds of pure lithium.(d)
• Cobalt ore grades average about 0.1%, thus nearly 30,000 pounds of ore.(e)
• Nickel ore grades average about 1%, thus about 6,000 pounds of ore.(f)
• Graphite ore is typically 10%, thus about 1,000 pounds per battery.(g)
• Copper at about 0.6% in the ore, thus about 25,000 pounds of ore per battery.(h)
In total then, acquiring just these five elements to produce the 1,000-pound EV battery requires mining about 90,000 pounds of ore. To properly account for all of the earth moved though—which is relevant to the overall environmental footprint, and mining machinery energy use—one needs to estimate the overburden, or the materials first dug up to get to the ore. Depending on ore type and location, overburden ranges from about 3 to 20 tons of earth removed to access each ton of ore.(i)
This means that accessing about 90,000 pounds of ore requires digging and moving between 200,000 and over 1,500,000 pounds of earth—a rough average of more than 500,000 pounds per battery. The precise number will vary for different battery chemistry formulations, and because different regions have widely variable ore grades.
It bears noting that this total material footprint does not include the large quantities of materials and chemicals used to process and refine all the various ores. Nor have we counted other materials used when compared with a conventional car, such as replacing steel with aluminum to offset the weight penalty of the battery, or the supply chain for rare earth elements used in electric motors (e.g., neodymium, dysprosium).(j) Also excluded from this tally: the related, but non-battery, electrical systems in an EV use some 300% more overall copper used compared with a conventional automobile.(k)
So that is, on average, 226,800 kg of ‘Mother Earth’ that has to be dug up and shifted for each EV battery in order to power the CCP dreams. You can bet your last dollar that the equipment used to dig up and move this amount of dirt is NOT going to be electrically powered.
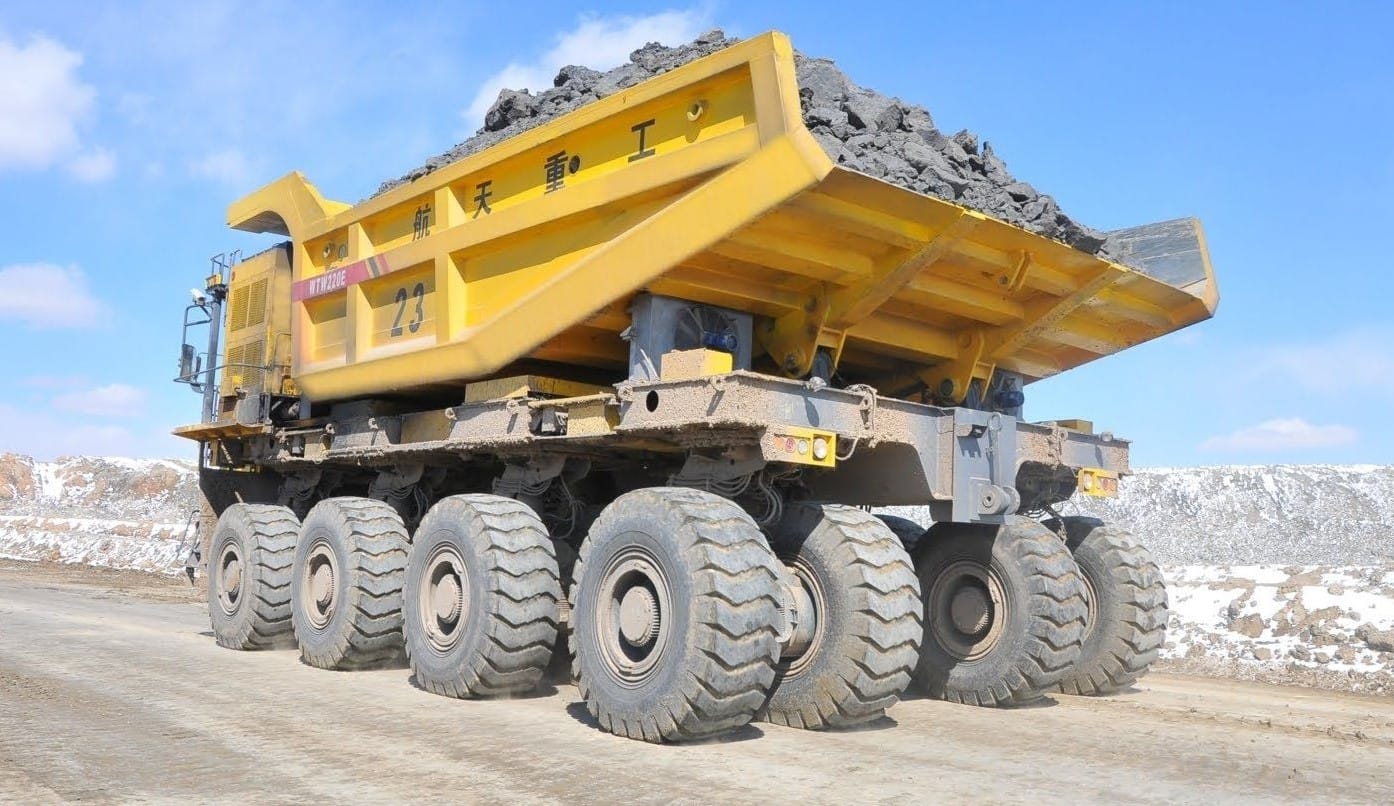
So how much is 226,800 kg? Well, just coincidentally, the rated load of the WTW220e pictured above is 220,000 kg. Rounding off, that is one truck load per EV battery.
But hey! We’re saving the planet!
Sources:
(a) Helena Berg and Mats Zackrisson, “Perspectives on Environmental and Cost Assessment of Lithium Metal Negative Electrodes in Electric Vehicle Traction Batteries,” Journal of Power Sources 415 (March 2019): 83–90.
(b) Marcelo Azevedo et al., “Lithium and Cobalt: A Tale of Two Commodities,” McKinsey & Company, June 22, 2018; Matt Badiali, “Tesla Can’t Make Electric Cars Without Copper,” Banyan Hill, Nov. 3, 2017; Amit Katwala, “The Spiraling Environmental Cost of Our Lithium Battery Addiction,” Wired, Aug. 5, 2018.
(c) Paul Gait, “Raw Material Bottlenecks and Commodity Winners,” in Electric Revolution: Investing in the Car of the Future, Bernstein Global Research, March 2017; Fred Lambert, “Breakdown of Raw Materials in Tesla’s Batteries and Possible Bottlenecks,” electrek.co, Nov. 1, 2016; Matt Bohlsen, “A Look at the Impact of Electric Vehicles on the Nickel Sector,” Seeking Alpha, Mar. 7, 2017.
(d) Hanna Vikström et al., “Lithium Availability and Future Production Outlooks,” Applied Energy 110 (2013): 252–66.
(e) John F. Slack et al., “Cobalt,” in Critical Mineral Resources of the United States—Economic and Environmental Geology and Prospects for Future Supply, USGS Professional Paper 1802, Dec. 19, 2017.
(f) Vladmir I. Berger et al., “Ni-Co Laterite Deposits of the World—Database and Grade and Tonnage Models,” USGS Open-File Report 2011-1058 (2011).
(g) Gilpin R. Robinson Jr. et al., “Graphite,” in Critical Mineral Resources of the United States.
(h) Guiomar Calvo et al., “Decreasing Ore Grades in Global Metallic Mining: A Theoretical Issue or a Global Reality?” Resources 5, no. 4 (December 2016): 1–14; Vladimir Basov, “The World’s Top 10 Highest-Grade Copper Mines,” mining.com, Feb. 19, 2017; EPA, “TENORM: Copper Mining and Production Wastes”: “Several hundred metric tons of ore must be handled for each metric ton of copper metal produced.”
(i) DOE, Industrial Technologies Program, Mining Industry Bandwidth Study, prepared by BCS, Inc., June 2007; Glencore McArthur River Mine, “Overburden.” The seven tons of overburden per ton of ore mined is highly variable.
(j) Jeff Desjardins, “Extraordinary Raw Materials in a Tesla Model S,” visualcapitalist.com, Mar. 7, 2016; Laura Talens Peiró and Gara Villalba Méndez, “Material and Energy Requirement for Rare Earth Production,” JOM 65, no. 10 (October 2013): 1327–40.
(k) Copper Development Association, “Copper Drives Electric Vehicles,” 2018.